熔體共混合設備
發布時間:2019-07-20 14:28:34 點擊次數:3666
將共混所需的聚合物組分在它們的黏流溫度以上用混煉設備制取均勻聚合物共熔體,然后再冷卻、粉碎或造粒的方法。熔體共混設備的種類有雙輥煉塑機、密煉機、混煉型單螺桿擠出機和雙螺桿擠出機等。目前應用最為廣泛的是雙螺桿擠出機。
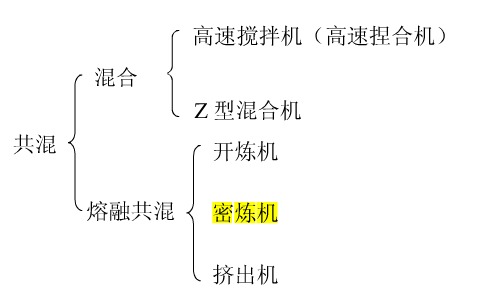
1.雙輥煉塑機
雙輥煉塑機是最早出現的混煉設備。其作用原理是通過兩根轉動的輥筒將物料混合或使物料達到規定的狀態。
雙輥煉塑機工作時,兩個輥筒相向回轉且速度不等。堆放在輥筒上的物料由于與輥筒表面的摩擦和黏附作用以及物料之間的粘接力而被拉入輥隙之內,在輥隙內物料受到強烈的擠壓與剪切,這種剪切使物料產生大的形變,從而增加了各組分之間的界面,產生了分布混合。該剪切也使物料受到大的應力,當應力大于(固相)物料的許用應力時,物料就會分散開。通過輥隙時,料層變薄且包在溫度較高的輥筒上,加上承受剪切時產生的熱量,物料即漸趨熔融或軟化。此過程反復進行,直至達到預期的熔融塑化和混合狀態,塑煉即完成,隨即可出片造粒或為其他設備供料。影響雙輥煉塑機熔融塑化和混合質量的因素有輥筒溫度、輥距、輥筒速度及速比、物料在輥隙上方的堆放量以及使物料沿滾筒軸線方向的分布和換位等。
雙輥煉塑機的優點有如下幾點:
(1)雙輥煉塑機工作時,經取樣可以直接觀察到物料在混合過程中的變化,從而能及時調整操作工藝及配方,達到預期的混合目的,特別是對那些其物性尚不完全清楚的物料用雙輥煉塑機比用其他混煉方法更有利于探索最適宜的工藝操作條件。
(2)在雙輥煉塑機上可隨時觀察到熱固性材料的固化程度。
(3)雙輥煉塑機結構簡單、混煉強度高、價格低廉。
(4)共混的聚合物原料在料度大小及粒度均一性方面不似干粉共混法哪樣嚴格,所以原料準備操作較簡單.
在混煉設備強剪切作用下,導致一部分聚合物分子降解并可形成一定數量的接枝或嵌段共取物,從而促進了不同聚合物組分之間的相容。
雙輥煉塑機的缺點有如下幾點:
(1)工人的勞動強度大,勞動條件差。
(2)能量利用不夠合理,物料易發生氧化。
密煉機
密煉機具有密閉的混煉室,操作安全,對物料混煉效果強,共混分散效果好,因此,避免了物料中的添加劑在混合過程中的氧化與揮發,并且可以加入液態添加劑。密煉機的密閉混合有效地改善了工作環境,降低了工人的勞動強度,縮短了生產周期,為自動控制技術的應用提供了條件。密煉機最早用于橡膠的混煉和塑煉,繼而又在塑料混合中得到了廣泛的應用。
密煉機的混煉室是一個斷面為M形的封閉空腔,內裝一對轉子,轉子兩端有密封裝置,用來防止物料從轉子轉軸處滲出。混煉室上部有加料及壓料裝置口,加料裝置由一個斗形加料口和翻板門組成。壓料裝置由上頂栓和氣缸組成,上頂栓與活塞桿及活塞相連接。卸料裝置設在混煉室下部,由下頂栓、下頂栓開閉裝置及鎖緊裝置組成。翻板門的開閉、上頂栓的提起與壓下均由氣動系統操縱,下頂栓的開啟與閉合以及鎖緊裝置的動作由液壓系統操縱。
密煉機在工作時,混煉室壁、轉子、上頂栓及下頂栓均須加熱或冷卻,因而配置有加熱冷卻系統。加熱介質一般是蒸汽或電加熱,冷卻介質是水。為了防止在混煉過程中轉子發生軸向移動或重新調整轉子軸向位置,當轉子軸承采用滑動軸承時,一般設有軸向調整裝置。當采用滾動軸承時,轉子軸向力由軸承承受,轉子與混煉室壁間的間隙一經調定,不必再設計軸向調整裝置。密煉機工作時,翻板門開啟,物料由加料門加入,翻板門關閉,上頂栓在氣壓驅動下將物料壓入混煉室,在工作過程中,上頂栓始終壓住物料。混合完畢后,下頂栓開啟,物料從排料口排出。排出的物料一般加入排料擠出機,可進行造粒或直接擠成片材。轉子是密煉機的核心部件,轉子結構是決定混煉性能的關鍵因素之一。傳統的密煉機轉子是兩棱橢圓形轉子,它的工作部分在任一斷面均呈橢圓形,轉子表面有兩條螺旋凸棱,凸棱凸出轉子工作部分兩端向中心延伸,一條左旋,一條右旋。兩條凸棱一長一短,螺旋角也不相同。轉子中心有空腔,可通入加熱或冷卻介質。
為了增大混合能力和生產效率,發展了多棱轉子,如三棱及四棱轉子。目前,在上述轉子的基礎上,又研究出了許多新型轉子,如在凸棱上開有周向溝槽的轉子,在表面裝有銷釘的轉子。這些新型轉子在減少能耗、提高混煉質量、降低混合溫度等方面均有突出優點。
強力加壓翻轉式密煉機主要特點:
1、本機裝置自動溫度及時間控制系統,操作精確、簡便,混煉可達到最佳分散及均勻度。
2、混合槽為可傾倒式,攪拌軸防漏采用干式機械軸封,使清洗換色簡便容易。
3、每次混煉時間約需6-10分鐘,工作效率為開煉機的2-3倍。
4、此密封式混合槽除可確保混合物品外,并可防止環境污染。
5、機器堅固耐用,故障率低,安裝操作保養容易,用電節省塑膠,EVA,TPR,PVC,彈性體高速造粒整套設備
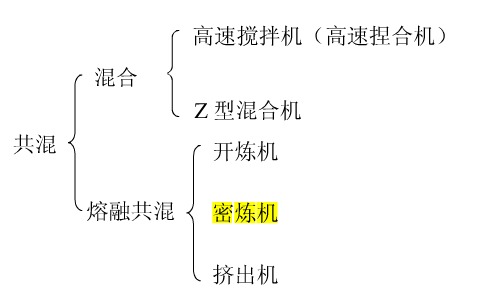
1.雙輥煉塑機
雙輥煉塑機是最早出現的混煉設備。其作用原理是通過兩根轉動的輥筒將物料混合或使物料達到規定的狀態。
雙輥煉塑機工作時,兩個輥筒相向回轉且速度不等。堆放在輥筒上的物料由于與輥筒表面的摩擦和黏附作用以及物料之間的粘接力而被拉入輥隙之內,在輥隙內物料受到強烈的擠壓與剪切,這種剪切使物料產生大的形變,從而增加了各組分之間的界面,產生了分布混合。該剪切也使物料受到大的應力,當應力大于(固相)物料的許用應力時,物料就會分散開。通過輥隙時,料層變薄且包在溫度較高的輥筒上,加上承受剪切時產生的熱量,物料即漸趨熔融或軟化。此過程反復進行,直至達到預期的熔融塑化和混合狀態,塑煉即完成,隨即可出片造粒或為其他設備供料。影響雙輥煉塑機熔融塑化和混合質量的因素有輥筒溫度、輥距、輥筒速度及速比、物料在輥隙上方的堆放量以及使物料沿滾筒軸線方向的分布和換位等。
雙輥煉塑機的優點有如下幾點:
(1)雙輥煉塑機工作時,經取樣可以直接觀察到物料在混合過程中的變化,從而能及時調整操作工藝及配方,達到預期的混合目的,特別是對那些其物性尚不完全清楚的物料用雙輥煉塑機比用其他混煉方法更有利于探索最適宜的工藝操作條件。
(2)在雙輥煉塑機上可隨時觀察到熱固性材料的固化程度。
(3)雙輥煉塑機結構簡單、混煉強度高、價格低廉。
(4)共混的聚合物原料在料度大小及粒度均一性方面不似干粉共混法哪樣嚴格,所以原料準備操作較簡單.
在混煉設備強剪切作用下,導致一部分聚合物分子降解并可形成一定數量的接枝或嵌段共取物,從而促進了不同聚合物組分之間的相容。
雙輥煉塑機的缺點有如下幾點:
(1)工人的勞動強度大,勞動條件差。
(2)能量利用不夠合理,物料易發生氧化。
密煉機
密煉機具有密閉的混煉室,操作安全,對物料混煉效果強,共混分散效果好,因此,避免了物料中的添加劑在混合過程中的氧化與揮發,并且可以加入液態添加劑。密煉機的密閉混合有效地改善了工作環境,降低了工人的勞動強度,縮短了生產周期,為自動控制技術的應用提供了條件。密煉機最早用于橡膠的混煉和塑煉,繼而又在塑料混合中得到了廣泛的應用。
密煉機的混煉室是一個斷面為M形的封閉空腔,內裝一對轉子,轉子兩端有密封裝置,用來防止物料從轉子轉軸處滲出。混煉室上部有加料及壓料裝置口,加料裝置由一個斗形加料口和翻板門組成。壓料裝置由上頂栓和氣缸組成,上頂栓與活塞桿及活塞相連接。卸料裝置設在混煉室下部,由下頂栓、下頂栓開閉裝置及鎖緊裝置組成。翻板門的開閉、上頂栓的提起與壓下均由氣動系統操縱,下頂栓的開啟與閉合以及鎖緊裝置的動作由液壓系統操縱。
密煉機在工作時,混煉室壁、轉子、上頂栓及下頂栓均須加熱或冷卻,因而配置有加熱冷卻系統。加熱介質一般是蒸汽或電加熱,冷卻介質是水。為了防止在混煉過程中轉子發生軸向移動或重新調整轉子軸向位置,當轉子軸承采用滑動軸承時,一般設有軸向調整裝置。當采用滾動軸承時,轉子軸向力由軸承承受,轉子與混煉室壁間的間隙一經調定,不必再設計軸向調整裝置。密煉機工作時,翻板門開啟,物料由加料門加入,翻板門關閉,上頂栓在氣壓驅動下將物料壓入混煉室,在工作過程中,上頂栓始終壓住物料。混合完畢后,下頂栓開啟,物料從排料口排出。排出的物料一般加入排料擠出機,可進行造粒或直接擠成片材。轉子是密煉機的核心部件,轉子結構是決定混煉性能的關鍵因素之一。傳統的密煉機轉子是兩棱橢圓形轉子,它的工作部分在任一斷面均呈橢圓形,轉子表面有兩條螺旋凸棱,凸棱凸出轉子工作部分兩端向中心延伸,一條左旋,一條右旋。兩條凸棱一長一短,螺旋角也不相同。轉子中心有空腔,可通入加熱或冷卻介質。
為了增大混合能力和生產效率,發展了多棱轉子,如三棱及四棱轉子。目前,在上述轉子的基礎上,又研究出了許多新型轉子,如在凸棱上開有周向溝槽的轉子,在表面裝有銷釘的轉子。這些新型轉子在減少能耗、提高混煉質量、降低混合溫度等方面均有突出優點。
強力加壓翻轉式密煉機主要特點:
1、本機裝置自動溫度及時間控制系統,操作精確、簡便,混煉可達到最佳分散及均勻度。
2、混合槽為可傾倒式,攪拌軸防漏采用干式機械軸封,使清洗換色簡便容易。
3、每次混煉時間約需6-10分鐘,工作效率為開煉機的2-3倍。
4、此密封式混合槽除可確保混合物品外,并可防止環境污染。
5、機器堅固耐用,故障率低,安裝操作保養容易,用電節省塑膠,EVA,TPR,PVC,彈性體高速造粒整套設備
上一篇:中央供料系統的輸送方式
下一篇:注塑機溫度控制